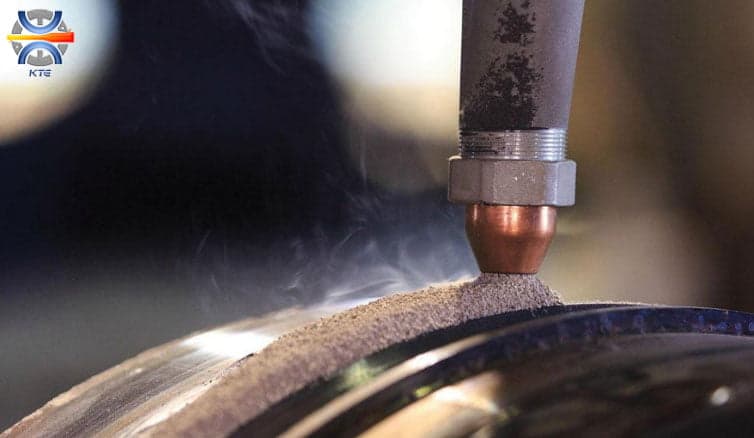
Welding creates a connection between different materials and objects with different techniques that can be used in different places, such as land and water. The first type of welding used worldwide was Shielded Metal Arc Welding or SMAW, which, although it had many applications, also caused problems. problems such as splashing of molten materials, radiation of dangerous rays, and creating environmental pollution occurred during work For this reason, a new method called submerged arc welding or SAW was created, which plays a vital role in heavy steel structures nowadays. Stay with us to learn more about this welding method.
What is Submerged Arc Welding?
There are two types of fusion and non-fusion welding, each of which has its subset. Submerged Arc Welding is a subset of Arc Welding and is considered a type of fusion welding.
This process is suitable for longitudinal and circular butt and corner joint welding. It is used to construct iron beams, heavy structures, railway wagons, pipelines, pressure vessels, etc. As the name of this type of welding suggests, It uses a powder containing unique minerals for welding, which is called flux. The reason for using this powder is the production of protective gases and slag or lubricant and adding alloy elements to the weld pool, which can be easily removed after welding. In this method, the heat loss is shallow because the welding powder completely covers the arc, and the welding efficiency is much higher.
The method of performing Submerged Arc Welding
In this type of welding, the guiding rollers guide the electrode wire through the contact tube, and the flux mass towards the connection is welded with continuous mechanical force. This electrode wire is usually low-carbon steel with a precise chemical composition that is melted in the weld zone and deposited during the joint. Meanwhile, flux is poured in front of the arc to create a shielding gas and slag, and the arc creates a layer of flux under the arc. After the solidification of the weld metal, the unmelted flux is collected by the collector suction system for reuse.
Types of Submerged Arc Welding
This type of welding is done in three ways:
1. Automatic method:
In this method, the inverter welding device automatically enters the electrode and flux into the welding path, and returning the flux to the device is also done with a tube placed right after the contact tube. This method does not require an operator.
2. Semi-automatic method:
In this method, a manual welding gun is used, guided by the welder, and transfers the electrode and powder. Still, the welding wire feeding is automatic, and the operator performs the welding process.
3. Machine method:
It is similar to the automatic method with the difference that starting and finishing the welding process, monitoring the speed, and adjusting the variables are all the operator’s responsibility.
Submerged Arc Welding machine parts:
The main parts of this device are:
Welding head
Flux hopper
Flux
Electrode wire feed unit
Electrode
Flux recovery unit
Consumable Electrode
Power Sources
Base metal
Electrode holder
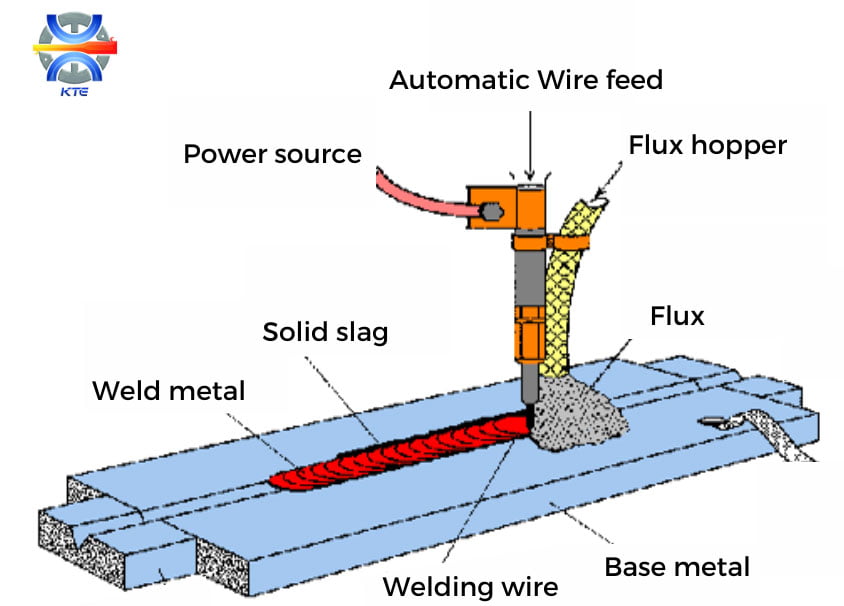
Influential factors in the Submerged Arc Welding process:
1. Electric current
Direct Current Electrode Positive (DCEP) is mainly used for low-depth submersible welding, so less oxidation occurs, and element recovery is more manageable. But Direct Current Electrode Negative (DCEN) is used when more welding depth is needed.
2. Voltage
The higher the voltage, the greater the width of the weld, and due to the increase in the length of the arc, the central part of the arc will be above the surface of the sample. For this reason, more welding powder melts, and the welding surface becomes smoother. But the low voltage increases the molten droplets at the tip of the electrode, which causes irregular welding dust without sufficient penetration or increasing slag confinement in the weld.
3. Welding speed
When the welding speed is high, its time reduces, and as a result of the input heat, the width and depth of the weld will be thinner.
4. Welding wire
The type of welding wire and its cross-sectional shape affects sub-powder welding. Changing the type of welding wire changes its engineering properties, and the round cross-section has smaller weld width and a greater penetration depth than the belt type.
5. Effective length of the electrode
The distance between the power source and the work surface is called the effective length of the electrode; the longer it is, the lower the penetration of the weld and the increase in the rate of deposition and melting.
6. Flux
Choosing the proper flux plays a vital role in the quality of SAW. Three types of flux are used in Submerged Arc Welding, which are:
Granular Flux
It usually comprises aluminum, calcium, magnesium, manganese, silicon, titanium, and zirconium oxides. This flux should be used with the right electrode and considering the properties of the desired metal in welding to perform suitable welding.
Bounded Flux
Bonded flux is produced by drying and slowly baking the composition, usually with a compound such as sodium silicate. As an advantage, bonded flux can contain alloying elements, offering flexibility for some applications and protection against rust.
Fused Flux
Fused flux is produced by melting the composition inside an electric furnace. The molten flux is formed into homogenous particles as it solidifies. It is excellent for creating consistent welds along the bead.
Advantages of using Submerged Arc Welding:
- It allows automatic and semi-automatic welding, and the operator’s influence is low on it.
- Fifty to ninety percent of the flux can be recovered and reused.
- There is minimal welding smoke and no welding spatter in the welding process.
- Welding speed is higher than other methods.
- High input heat and increased penetration depth make it suitable for welding thick parts.
- Joints can be welded with a shallow groove, so less filler metal is consumed.
- Due to the protective role of flux, this type of welding can also be used in the wind.
Disadvantages of using Submerged Arc Welding:
The welding process is not visible to the operator, and he cannot see welding defects.
Welding is done only in the horizontal and flat direction.
Burns metals with a thickness of less than 4/8 and cannot weld them.
The metal edges that will be welded must be immaculate and tidy. Because the flux might burn irregular edges.
Impurities in the flux cause porosity in the weld.
We can’t use Submerged Arc Welding on cast iron, aluminum, magnesium, and zinc alloys.
Slags must be collected each time.
Kian Tarash Spadana is ready to provide any Submerged Arc Welding، Cladding, and Hard facing services with up-to-date equipment.